We use cookies to ensure we give you the best experience on our website. By clicking Agree you accept our Privacy and Cookies Policy.
What is HMI development, and why is it trending now?
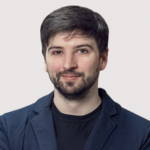
Yuriy Horak
Author
February 13, 2025
Date
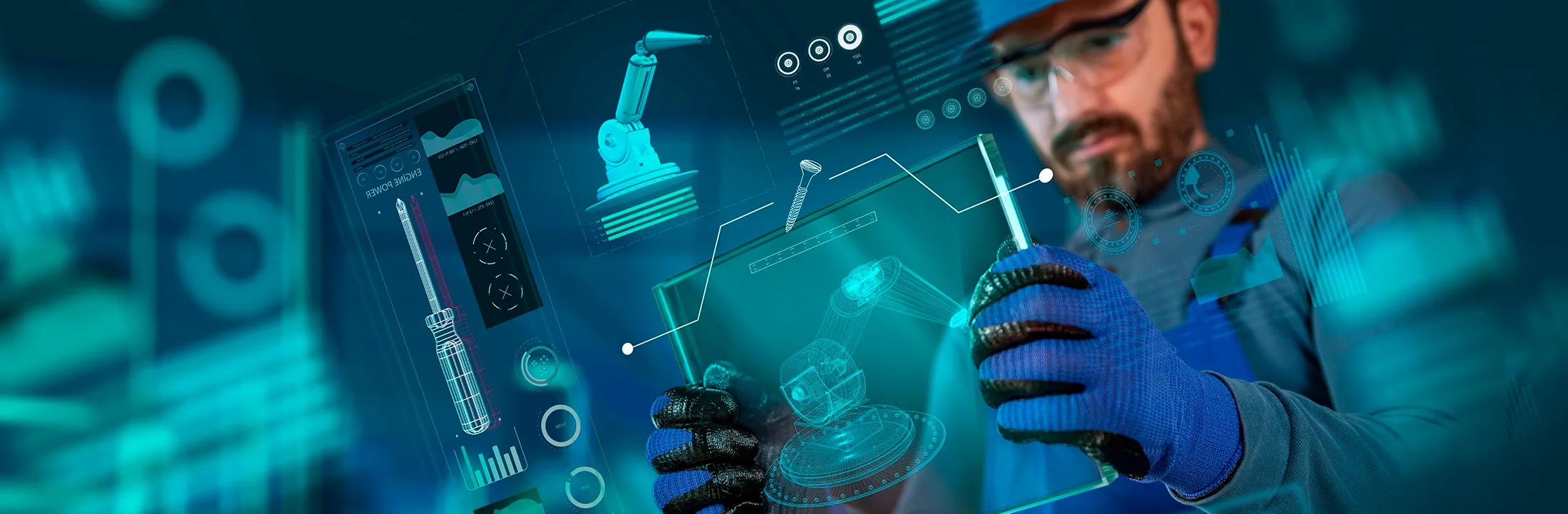
15 minutes read
Content
The current industrial revolution — Industry 4.0, the Fourth Industrial Revolution, or 4IR — is certainly digital. It’s an era of connectivity, advanced analytics, automation, and manufacturing technologies that have been transforming businesses worldwide for years now. This wave of change has spread far beyond the manufacturing sector and holds unimaginable potential for operations and the future of production.
In this context, we talk about Human Machine Interfaces (HMIs) — the ones connecting humans and machinery, leading to maximized efficiency and improved safety, and opening the possibilities never considered before.
The definition of HMI
A Human Machine Interface (HMI) connects a human interface module with the machine, device, or system to reach synergy and allow a user to interact with a device or mechanism, control it and monitor in the industrial processes.
HMIs are usually used for data visualization, time or progress tracking, KPI overseeing, input/output monitoring, and other purposes, depending on the field of application and the type of software. Many of these systems work similarly to technologies we interact with in everyday life but on a much bigger scale. The most prominent HMI examples include built-in screens on machines, computer monitors, and tablets.
In this article, we explain what HMI software is, what are the benefits and examples of these interfaces, and how Human Machine Interfaces are shaping the future of almost every field, from industrial to education.
HMI software: Core components and diverse types
Human-Machine Interface (HMI) software serves as the operational nexus between human operators and industrial machinery. Its functionality relies on a sophisticated interplay of components and manifests in various architectural types, each suited for distinct operational environments.
Core HMI software components
- Operating System (OS): The foundational layer managing hardware resources and providing the execution environment for HMI applications. Common industrial OS platforms include Windows Embedded, Windows CE, and Linux Embedded, offering stability and real-time capabilities.
- HMI Programming Software: Specialized tools utilized for the design of user interfaces, configuration of machine connectivity (e.g., with PLCs), and programming of control and monitoring functions. Examples include Siemens WinCC, Rockwell Automation FactoryTalk View, and Mitsubishi Electric GT Designer. These environments facilitate graphical interface creation, alarm management, data logging, and recipe management.
- Communication Protocols: Essential for data exchange between the HMI and connected devices (PLCs, sensors, drives). Standard industrial protocols like Modbus TCP/IP, Ethernet/IP, Profinet, Profibus, and OPC UA ensure seamless interoperability and data integrity across diverse hardware.
Diverse HMI software types
HMI solutions are categorized based on their deployment and interaction models, offering flexibility to meet varied industrial requirements:
- Standalone HMIs: Self-contained units with integrated hardware and software, designed for localized control and monitoring of a single machine or process. They are robust and perform independently of central networks.
- Networked HMIs: Integrated into broader industrial networks, allowing multiple HMIs to share data and communicate with various PLCs or SCADA systems across a facility. This enhances centralized oversight and collaborative operations.
- Cloud-Based HMIs: Leverage cloud infrastructure for data storage, processing, and remote access. This architecture facilitates global accessibility, enhanced data analytics, scalability, and simplified maintenance, enabling monitoring and control from any internet-connected device.
- Web-based HMIs: Utilize standard web browsers for interface display and interaction, eliminating the need for client-side software installations. They offer platform independence and ease of deployment, allowing access from various devices including PCs, tablets, and smartphones.
- Mobile HMIs: Specifically designed for mobile devices (smartphones, tablets), offering flexibility for operators to monitor and control systems on the go. These typically connect wirelessly and provide essential data visualization and control functionalities.
- Embedded HMIs: Integrated directly into machines or devices, providing a compact and purpose-built interface. They are common in specialized equipment where space or cost constraints are significant.
How it works?
What is HMI software if not a prominent example of a bridging technology? HMI software meaning lies in connecting Programmable Logic Controllers (PLCs) and input/output sensors, enabling data exchange and providing users with actionable insights. Depending on their configuration, HMI screens can be tailored for basic tasks like monitoring and tracking or for advanced operations, such as controlling machine functions or optimizing production rates.
HMIs centralize and digitize industrial processes and, therefore, play a critical role in improving overall operational efficiency. They can monitor and manage alarms and integrate with systems like supervisory control and data acquisition (SCADA), Enterprise resource planning (ERP), and manufacturing execution system (MES) — all from a single interface. HMI technology delivers real-time data directly from programmable logic controllers (PLCs) to an intuitive display, reducing reliance on archaic methods as well as the chance of errors and inefficiencies related to manual interventions.
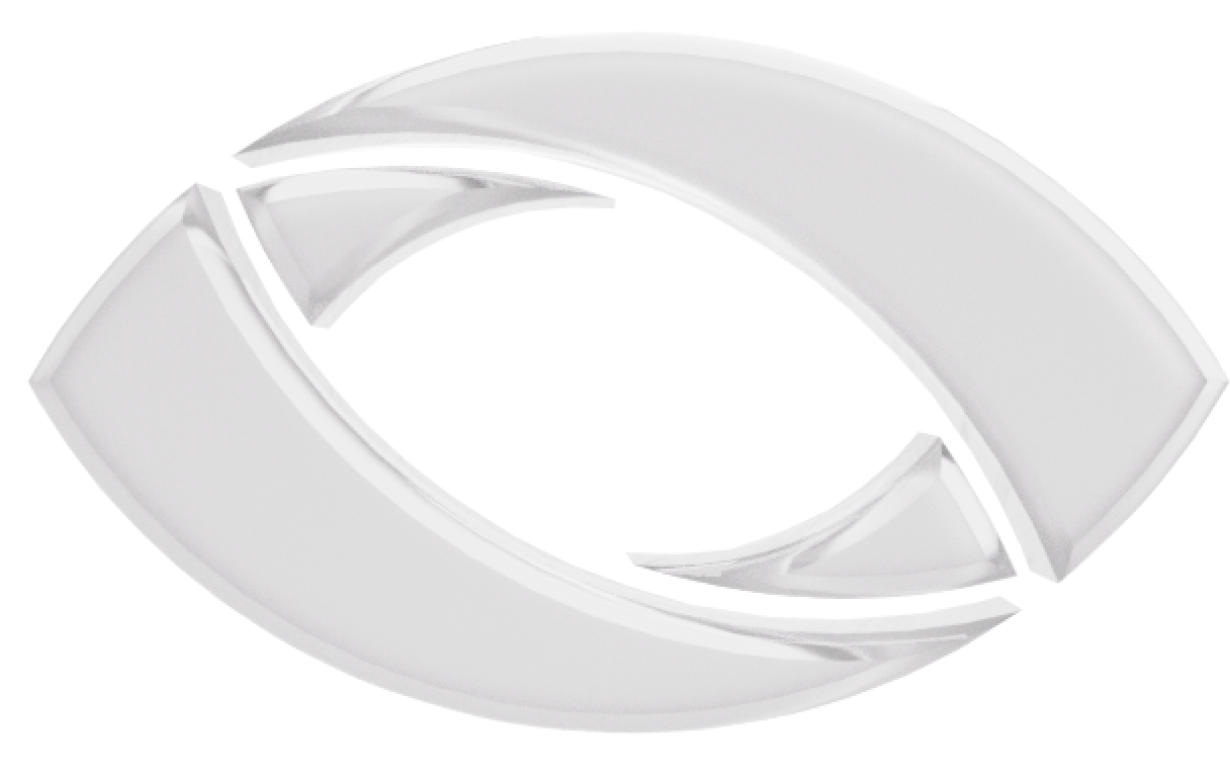
Consult Our HMI Experts Today
Get a Custom HMI Development Quote
The HMI software development process
Developing effective HMI software is a structured endeavor that spans several critical phases, ensuring the final product meets operational requirements and enhances user interaction.
- Requirements analysis and scoping: This initial phase involves a deep dive into the client’s operational needs, existing infrastructure, and specific objectives. Key considerations include the types of machinery, data points for monitoring, control functionalities required, user roles and access levels, and environmental conditions. This phase culminates in a detailed functional specification.
- User interface (UI) / User experience (UX) design: Based on the gathered requirements, designers create intuitive and efficient interfaces. This includes wireframing, prototyping, and graphic design, focusing on clear data visualization, logical navigation flows, and ergonomic interaction. Adherence to industry standards like ISA 101 for HMI design is crucial for consistency and operator performance.
- System architecture and database design: Engineers define the HMI software’s underlying architecture, selecting appropriate hardware platforms, operating systems, and communication protocols. Concurrently, the database structure is designed to efficiently store and retrieve operational data, historical trends, and alarm logs.
- Development and programming: This phase involves writing the code for the HMI application, integrating it with PLCs and other control systems, and implementing the designed UI/UX. This includes configuring data tags, scripting control logic, setting up alarm conditions, and developing data trending and reporting functionalities.
- Testing and quality assurance (QA): Rigorous testing is conducted to ensure the HMI software is robust, reliable, and performs as expected. This includes functional testing, integration testing, performance testing, and user acceptance testing (UAT) in a simulated or actual operational environment to identify and rectify any bugs or discrepancies.
- Deployment and integration: Once tested and validated, the HMI software is deployed onto the target hardware and integrated with existing industrial systems (e.g., SCADA, ERP, MES). This often involves configuring network settings, establishing communication links, and ensuring seamless data flow.
- Training and support: Post-deployment, comprehensive training is provided to operators and maintenance personnel to ensure proficient use of the new HMI system. Ongoing technical support and maintenance services are crucial for sustained performance, addressing issues, and implementing future enhancements.
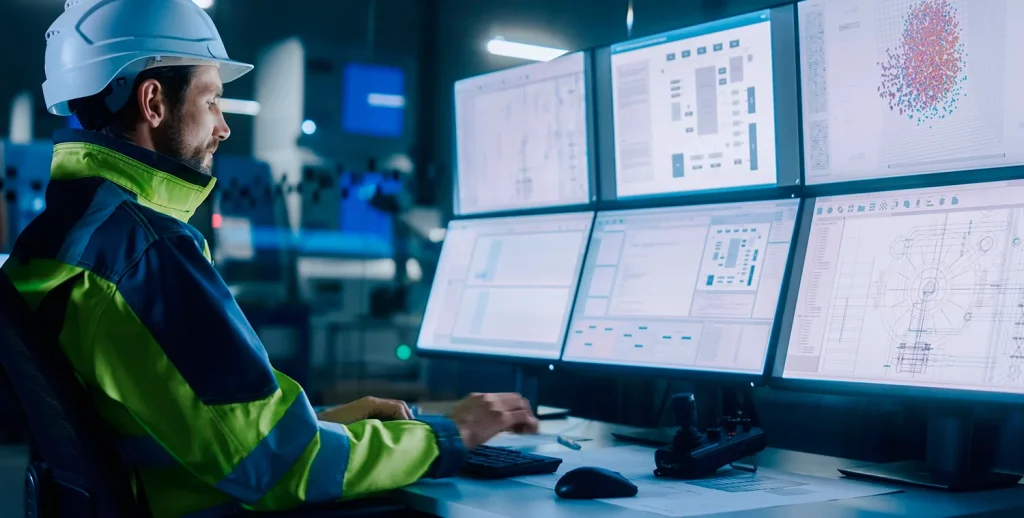
What are the benefits of HMI software?
Ease of use
To embrace the difference in use, compare operating numerous buttons, levers, switches, dials, LED lights, and gauges to a touchscreen. The interface is intuitive and responsive, streamlined and user-friendly. It’s easy to learn and to operate, with much fewer chance of mistakes and mechanical errors.
Increased productivity and efficiency
The need to divide your attention into numerous control and monitoring functions dramatically decreases productivity. It’s physically and mentally overwhelming and requires extensive experience and constant coordination. With a single dashboard, the centralized platform eliminates the need to move across panels, boosting efficiency and reducing the number of errors, delays, and stressful situations.
Improved employee safety
Operating heavy machinery is not only a difficult but a potentially dangerous task. With HMI systems, operators can keep the distance from machines while not losing in productivity and keeping control. Moreover, while working from distance, they gain better visibility and monitor operations with higher precision. Additionally, HMIs allow for remote visual inspections thanks to cameras that broadcast real-time images to the operator’s device. This means there is no longer a need for close physical proximity to potentially dangerous machinery.
Increased reliability
Machine reliability is the priority number one for industrial facilities, since this is the subject of efficiency and safety. With HMI, operators get access to the real-time data about machines operability and condition, collected by IoT sensors, gaining the possibility to spot animalities, fix issues, and prevent problematic or dramatic outcomes.
Reduced costs
All the advantages of HMI software collectively result in significant cost reductions. First and foremost, thanks to reduced maintenance expenses and faster staff training. Early spotting of issues lowers the cost of repairs and replacements, as well as downtime costs. Considering the ease of use and user-friendly interfaces, it’s not necessary to look for expensive, experienced operators – they can be trained in-house.
High return on investment (ROI)
A strong return on investment (ROI) makes HMI even more attractive for industrial facilities. The initial software implementation, HMI development, and mobile devices costs get quickly outweighed by the reduced operational costs and boost in productivity. Enhanced machine reliability, streamlined processes, and reduced training times — all together result in saving valuable resources and investment return.
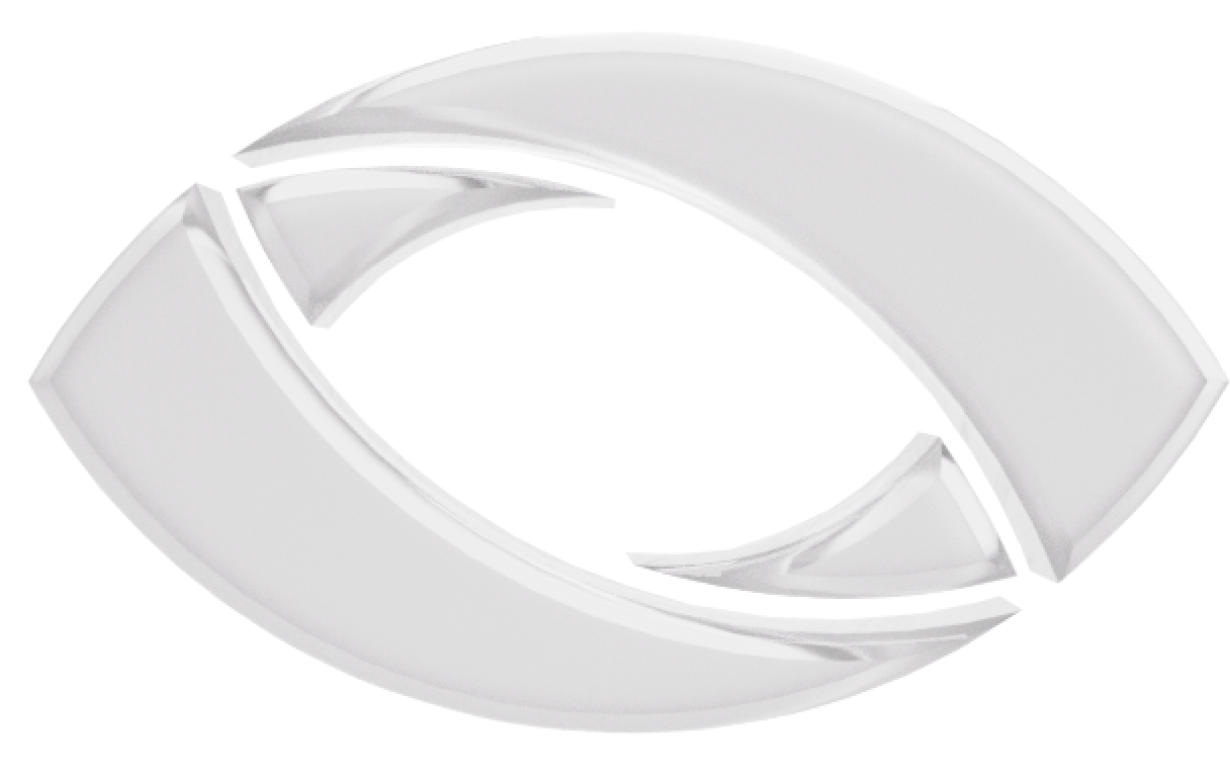
Stay ahead in smart manufacturing
Discover how Blackthorn Vision’s intuitive HMI solutions
Navigating challenges in HMI implementation
While HMI solutions offer significant advantages, their implementation can present specific challenges. Recognizing and addressing these proactively is key to a successful deployment and maximizing return on investment.
- Data integration and legacy systems: Integrating new HMI software with existing legacy machinery and diverse proprietary systems can be complex due to disparate communication protocols and data formats.
- Solution: Employ robust integration platforms and middleware that support a wide array of industrial protocols. Custom API development or utilizing standardized interfaces like OPC UA can bridge compatibility gaps. Phased implementation strategies also mitigate disruption.
- Cybersecurity vulnerabilities: As HMI systems become increasingly interconnected and cloud-enabled, they present potential entry points for cyber threats.
- Solution: Implement a multi-layered security strategy, including network segmentation, robust firewalls, end-to-end encryption, multi-factor authentication, and regular security audits. Adherence to industrial cybersecurity standards (e.g., IEC 62443) is paramount.
- User adoption and training: Operators accustomed to traditional control methods may resist new HMI systems, leading to initial productivity dips and errors.
- Solution: Involve end-users in the UI/UX design process to foster ownership. Provide comprehensive, hands-on training tailored to different user roles. Emphasize the long-term benefits and ease of use to encourage adoption.
- Scalability and future-proofing: Ensuring the HMI system can scale with future business growth and integrate emerging technologies (e.g., advanced AI/ML models) is a common concern.
- Solution: Design modular and flexible HMI architectures that support easy expansion and upgrades. Utilize open standards and frameworks that facilitate integration with new technologies.
- Real-time performance and reliability: In critical industrial applications, any delay or instability in the HMI can have significant operational and safety consequences.
- Solution: Optimize HMI software for low latency and high responsiveness. Implement redundant systems and robust error handling mechanisms to ensure continuous operation and data integrity. Thorough testing under various load conditions is essential.
How HMI software enables smart manufacturing
HMI software development is at the heart of the smart manufacturing revolution. It bridges the gap between technology output and human decision-making, opening the door for businesses to greater efficiency, flexibility, and scalability in their operations. Here is how it’s being done:
1. Real-time monitoring and visualization
With HMI software, operators gain access to well-structured, intuitive, data, collected in real-time and displayed in form of customized charts and maps. Thanks to such visualization, users gain a power of early spotting of issues, controlling productivity, and gaining valuable insights, necessary for business development and more informed decision making.
2. Simplified control and interaction
HMI systems offer more precise control and interactions with machines and automation systems. From adjusting setting to running diagnostics, fine-tuning operations and quickly interrupted issues, this simplified interactivity reflects in enhanced productivity and product or service quality.
3. Easy and fast data integration
One of the key characteristics of smart manufacturing is vast amount of data, generated at every stage of production. HMI software comes in handy when this data needs to be analyzed and integrated. Combined with the Industrial Internet of Things (IIoT), HMI delivers insights that operators can later use to optimize workflows, address issues, improve efficiency, adjust processes, and prevent potential mistakes.
4. Remote monitoring and maintenance
Most HMI systems include cloud connectivity that enables for a remote machine monitoring and control. Thanks to this, operators can run diagnostics ad address issues remotely, from any location, reacting quickly and supporting predictive maintenance strategies. This reflects in lower repair and downtime costs and uninterrupted production.
How HMI shapes the future of smart manufacturing
The next generation of HMI technology will redefine smart manufacturing. With AI, AR, IoT, and intuitive controls at its core, HMI will enhance productivity and empower operators to navigate the complexities of the industrial revolution.
AI and ML
These systems can analyse data in real time, define patterns, predict potential failures, recommend process optimizations, and autonomously adjust machine settings to reach better performance.
Augmented Reality (AR)
AR-enabled interfaces allow for overlaying digital information onto the physical environment, providing real-time guidance for troubleshooting, maintenance, and task control. Such an immersive experience allows operators to manage complex processes more precisely and efficiently, reducing the chance of errors.
Industrial Internet of Things (IIoT)
As the Industrial Internet of Things (IIoT) grows, HMI systems must handle larger and larger amounts of data generated by connected devices. To cope with this, HMIs integrate with IoT networks, enabling centralized control of multiple machines and processes. This integration simplifies operations in even the most complex industrial ecosystems.
Voice and gesture controls
Voice recognition and gesture control make HMI systems even more intuitive and accessible. Hands-free operation improves safety and efficiency, and voice control allows for even faster change-making. The development of these technologies will allow operators to execute commands quickly and accurately without manual interactions.
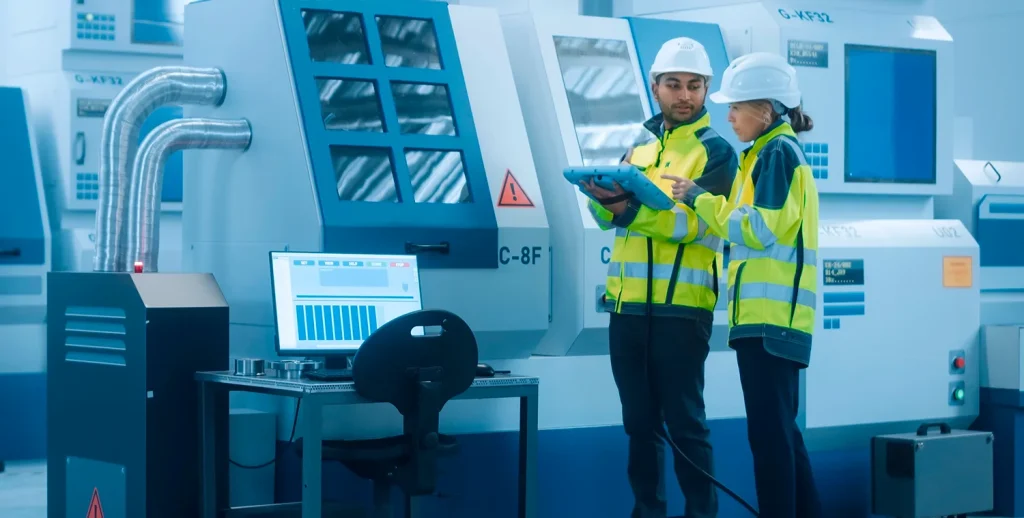
Human Machine Interface examples
While all HMIs serve a similar grand purpose, their designs and configurations vary, assisting in different operational needs. The following are examples of the most common types of HMI devices.
Touchscreen HMIs
While traditional interface panels with hardwired buttons have their uses, touchscreen HMI panels dominate when it comes to flexibility and user experience. These interfaces are so prevalent that they’ve become synonymous with HMI for many people. Touchscreen panels seamlessly integrate user input and display output, allowing designers to create custom screens tailored to specific tasks.
Web HMIs
Unlike traditional HMIs, Web HMIs rely on centralized servers for data storage and processing, eliminating the need for local hardware configurations. This setup reduces installation complexity and ensures that updates can be managed centrally, minimizing maintenance requirements.
Headless HMIs
Headless HMIs offer a unique solution for application modernization where a built-in screen is unnecessary or impractical. These devices omit the screen, instead transmitting video output via HDMI or network connections. This significantly reduces the size of the unit, which is incredibly beneficial in limited spaces.
Industrial PCs
While Industrial PCs may not fit the traditional definition of an HMI, they are worth mentioning for their versatility and power. These devices can perform all the functions of an HMI and much more. Industrial PCs allow for easy hardware upgrades, extending their lifespan and reducing long-term costs. Available in both panel-mounted and traditional configurations, Industrial PCs are well-suited for demanding applications that require robust performance and scalability.
Fields and applications of HMI
Thanks to its versatility, HMI technology gets adopted across the fields, bringing countless benefits and optimizing processes. The most common application of HMI technology is in monitoring industrial equipment and machinery, especially in factories and other industrial settings. Human Machine Interface systems display real-time data about different processes and allow operators to make fast and informed decisions.
In the healthcare sector, HMIs are used in devices such as infusion pumps, patient monitors, and diagnostic equipment. These interfaces allow healthcare professionals to interact with complex systems, ensuring the most accurate patient care. HMIs also improve connectivity among devices and systems, enhancing efficiency and precision in healthcare.
ATMs and other banking interfaces leverage HMI technology to facilitate secure financial transactions. Customers can use these systems to check balances, transfer funds, make withdrawals, and perform other banking operations quickly, securely, and conveniently.
Touchscreen kiosks are a very common example of HMI application in public spaces. These interfaces provide information and services at transportation hubs, museums, retail locations, and office buildings.
In educational environments, HMI technology powers tools like interactive whiteboards and tablets. These interfaces improve engagement and collaboration in classrooms, making learning experiences more engaging and accessible for students and teachers.
With the advent of smart home technologies and building automation, HMIs are now leaders in managing heating, lighting, and security systems. Smartphone apps, touchscreens, and voice-controlled devices allow users to monitor and control entire buildings easily and remotely, improving energy efficiency and security and saving costs.
In summary
Industry 4.0 is racing, and HMI development is on the rise. With smart manufacturing and HMI industrial automation, those systems act as the crucial bridge between human operators and machinery. As industries continue to advance, HMI technology will evolve alongside emerging innovations such as AI, augmented reality, and IoT, driving further improvements in safety and productivity.
The future of HMI promises even more intuitive and powerful tools, empowering industries to meet the demands of an increasingly automated and interconnected world. Contact us to discuss HMI development and define HMI that will make your system operations more efficient, convenient, and competitive.