We use cookies to ensure we give you the best experience on our website. By clicking Agree you accept our Privacy and Cookies Policy.
Smart manufacturing technology and trends for 2025 and beyond
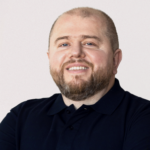
Volodymyr Yakubovskyy
Author
March 3, 2024
Date
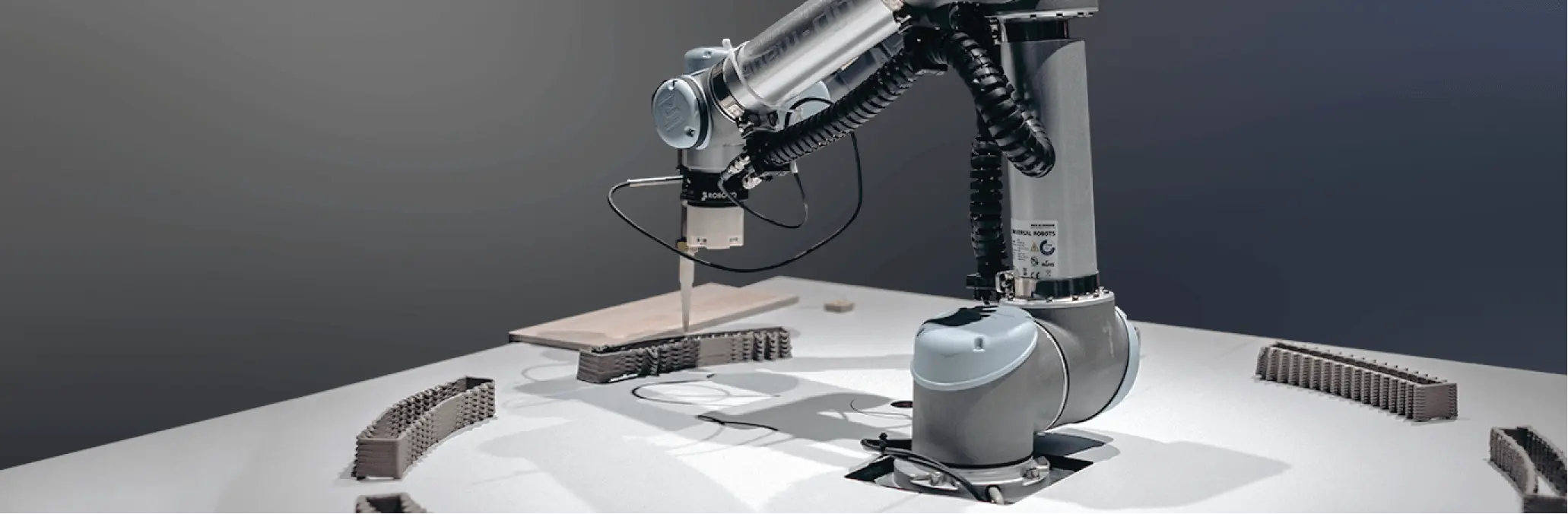
10 minutes read
Content
Manufacturing has undergone a remarkable transformation throughout its history – from manual production to AI-controlled processes. In one of our previous articles, we wrote about hyper-automation penetrating many spheres. Now let’s look at technologies that make a factory “smart,” as well as the key trends that shape manufacturing today.
The overall tendency is to make all processes transparent, predictable, and fully manageable in real-time for maximum profitability and workplace safety. The market necessitates innovations: supply chains are getting more complex; manufacturers are under pressure for a shorter time-to-market for new products. Integrated software applications can now perform different processes simultaneously – not in chronological sequence as before – order raw materials, schedule manufacturing, assemble a product, launch marketing campaigns, and even start pre-sales. Cutting-edge technologies, such as IoT, cloud services, Virtual and Augmented Reality, Collaborative robots, AI and ML are redefining business models and processes.
The “smart” approach also requires a digital mindset. However, people are often intimidated by new technologies, especially the prospect of being replaced by robots and losing their job. Companies and some national governments are making efforts to foster the culture of innovation, educate and upskill the workforce.
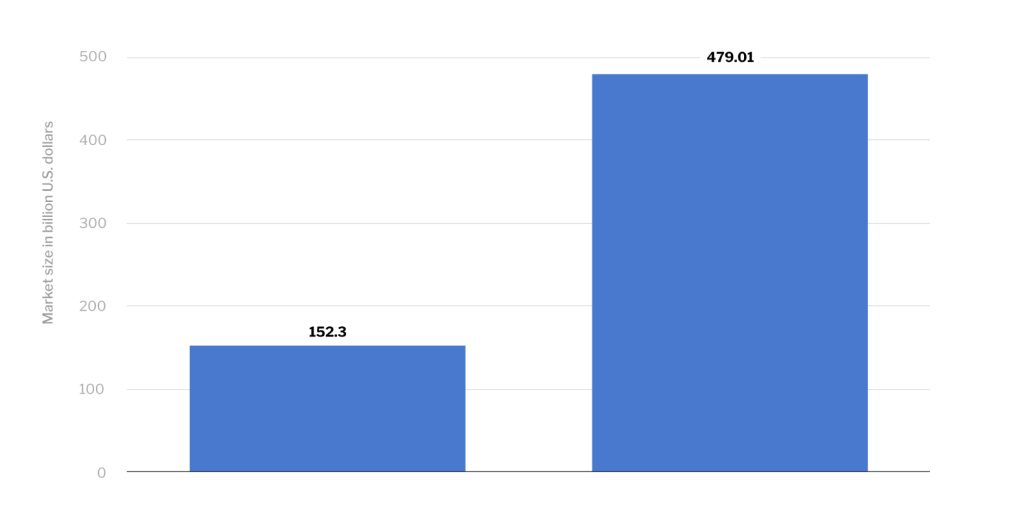
Source Statista
Industry 4.0
The fourth era of manufacturing through data-driven automation and machine learning is referred to as industry 4.0. The term Fourth Industrial Revolution was introduced to a wide audience in 2015 by Klaus Schwab, executive chairman of the World Economic Forum. He used it to describe how new cyber-physical systems function (biology, hardware, and software) to optimize processes and create value. The powerful combo of these cyber systems with the Internet of Things and the Internet of System gave rise to smart factories. During the whole product lifecycle, state-of-the-art-technology improves operational visibility, decreases cost while accelerating production time and elevating customer care. Industry 4.0 is characterized by a new level of connectivity between machines that are now capable of collecting, sharing information, and making decisions without humans. Machine-to-machine communication allows them to operate almost independently – respond and adjust their operations through smart feedback loops. Integrated systems of connected machines also generate enormous amounts of data, including unstructured datasets, e.g., images. AI derives patterns and insights from these data and suggests how to optimize operations, logistics, and supply chains. For instance, delayed shipments due to adverse weather conditions may change manufacturing priorities. The more data they process, the smarter they get through experience – this is the essence of Machine Learning.
Industrial internet of things
The IoT has been on the list of growing trends for a decade. It is now a must-have in manufacturing, also known as IIoT – Industrial Internet of Things – an umbrella term for sophisticated networks of industrial systems that provide data through the internet for remote monitoring analysis. Sensors and advanced communication technologies are the core elements of IIoT. It is predicted to dominate the smart factory scene by 2025 as it enables many other industrial technologies., e.g., distributed control systems.
IIoT solutions let users view real-time data from any asset in a historical context, detect potential performance problems before they arise, track trends, and get insights for better business decisions. They also help to create new business models and boost revenue.
3D printing (additive manufacturing)
This technology dates to 1981 when Hideo Kodama from Nagoya Municipal Industrial Research Institute introduced a rapid prototyping system based on layers of photopolymers. Modern 3D printing is the result of the amazing digital evolution of imaging, architecture, engineering, and software development. Also referred to as “additive manufacturing” or “rapid prototyping,” it enables fast production of more lightweight and durable parts and systems and makes production way more flexible and efficient. Manufacturers use CAD (computer-aided-design) software, three-dimensional object scanners, and a variety of materials to create objects. The 3D printing processes – vat polymerization, powder bed fusion, material extrusion, sheet lamination, material jetting, directed energy deposition, binder jetting, etc., differ depending on how layers of an object are built.
One of the outstanding merits of this technology is prototyping – a quick and affordable way to test and upgrade new products. It has also cheapened and accelerated tooling – the production of molds and fixtures for manufacturing heavy equipment, which is critical for many spheres. For instance, in the aerospace industry, additive manufacturing makes parts 40-60% lighter, which leads to reduced fuel consumption, and respectfully, lower carbon dioxide emissions. Compared to conventional manufacturing, which includes assembly of multiple components, 3D printing allows integrating much more functionality in one part. Industrial designs of any complexity can be implemented and optimized within very short timeframes as no tools are needed.
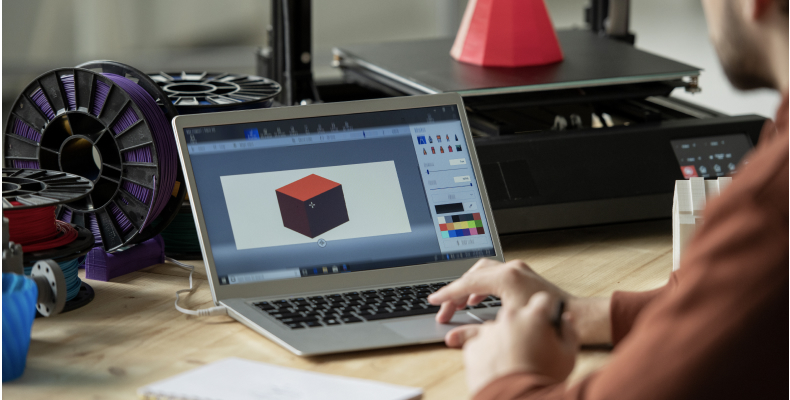
The transition from B2B to B2C and PaaS
The increasingly popular mindful consumption focuses on sustainability, respect for local communities, and business ethics. Manufacturers are starting to follow this trend and step back from the linear economy approach, where they sell the product once and are no longer responsible for it. In the PaaS business model (Product as a service (PaaS) or Product-Service systems), consumers buy a service subscription together with the product. The new business model is the combination of product and repair/ replace/ upgrade service contracts, which stimulates the manufactures to continuously improve the quality in close interaction with the consumers. It is possible thanks to digital data obtained from consumers during the product service life through software overlooking the customer process. This model is of circular economy, where the product returns to the manufacturer after the end of its usage to be recycled. Perhaps it will even get a new life.
There has also been a marked transition from the B2B to the B2C model. Manufacturers want to sell directly to consumers without any third-party mediators. It has the following benefits:
- shorter time to market
- full control over pricing, higher profits
- strong brand image
- better customer engagement and quick feedback
Touchless service model
Covid-19 has also accelerated the adoption of the touchless service model, enabled by Augmented and Virtual reality tools. Now customers do not need technicians to install or repair equipment – they can do it on their own with AR or VR devices provided by manufacturers.
Predictive maintenance
A single equipment failure may lead to consequent fatal damage, unplanned downtime, and thousands of dollars losses. Therefore, continuous machine condition and performance tracking, and predictive analytics are crucial in preventing accidents. IoT sensors provide real-time data that are automatically compared to a set of performance standards to detect any deviations. If the values are critical, the system alerts the operator on the need for maintenance. This approach considerably prolongs the life of equipment, prevents unscheduled outages, and minimizes downtime, saving precious time and resources.
Mobile robotics
Mobile robots are used across many industries, from agriculture to logistics and healthcare. They are often a crucial part of automation at factories and plants. Autonomous mobile robots interact with human operators through a system of sensors to adjust their performance to eliminate any risk and ensure worker safety. They carry out inspection and rescue tasks with hazardous substances or high-risk environments. In logistics, they are indispensable for handling heavy loads. For instance, the agile, mobile robot from Boston Dynamics – Spot is used for inspection and data capture missions in the construction, utilities, oil and gas, mining industries, etc. The price starts at $74,500.
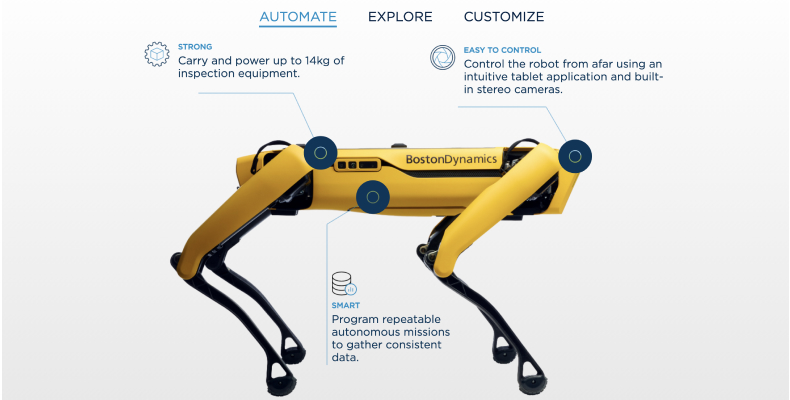
Source Boston Dynamics
Enterprise resource planning
Many enterprises face huge volumes of siloed data and a lack of synergy between departments, creating bottlenecks. The solution is an enterprise resource planning system. ERP is a management software system that integrates key business processes. It collects, processes, and interprets data on resources – finance, production capacity, raw materials, supply chains, customer service, etc., in real-time. The term was introduced by the Gartner Group in the 90-ies to describe the evolution of material resource planning, and later on – manufacturing resource planning and computer-integrated manufacturing. Now ERP is used to describe tools and applications, including those beyond manufacturing, which share a common database and can be accessed through a single interface. According to Gartner, the ERP market reached 39 billion US dollars in 2020 and is demonstrating steady growth.
ERP benefits for an enterprise:
- Quick and easy access to any enterprise data
- Accurate and comprehensive reporting
- Convenient knowledge sharing
- Easier collaboration between teams/departments
- Better planning, budgeting, forecasting, and stakeholder communication
- Improvement of business processes
- Acceleration of business innovations
- Standardization of processes
- Economy of IT costs
- Error-free transactions and production
- Enhanced enterprise efficiency
- Elimination of many manual tasks
Inventory management
Manufacturing Inventory includes raw materials, work-in-process, and ready products. Effective inventory management is critical for the whole supply chain and the profitability of the business on the whole. Modern software systems perform the following functions:
- Prevention of manufacturing and fulfillment cycle errors
- Optimization of physical space and cost per square meter
- Lowering inventory shipment and transportation time
- Effective documentation management (bill of materials, work of orders, purchase order)
- Calculation of the products final cost
- Integration with accounting software (invoices, packing slips)
Asset tracking
Digitalization of asset management is one of the keys to optimizing asset usage efficiency and availability. The tracking software and hardware (location tags), known as Real-Time Location System (RTLS), provide data on a physical asset – its location and utilization at a factory. For instance, manufacturers can detect how often a piece of equipment is used, what the usage patterns are, and if it is authorized. These data insights serve to reduce inventory waste, decrease idle time, improve transportation schemas, enhance the Work-in-Progress (WIP) flow, etc. Employees’ movement on the floor can also be tracked for maximizing their productivity and decreasing labor costs.
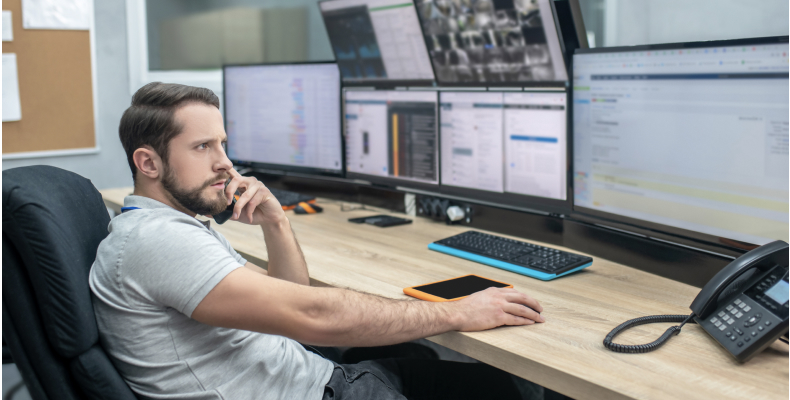
Warehousing cost reduction
Warehouse automation is a crucial step towards higher profitability. It can be implemented by using RFID portals, voice-directed picking systems, barcode readers in combination with warehouse management systems – the software that complements inventory management and contributes to supply chain visibility.
Forecasting accuracy
Forecasting demand is an essential part of planning in manufacturing, especially for products with short shelf life. However, forecasting accuracy is only one of the manufacturing elements that result in positive business outcomes. Lead times, batch size, planning cycles are equally important and require a holistic approach. Manufacturers used to rely on historical data and intuition to predict consumer demand. Now it is IoT and ML that take forecasting to a new level. IoT sensors on the factory floor and throughout the whole supply chain provide an unprecedented level of transparency and visibility. Integration software carries out a realistic assessment of manufacturing processes and blends this information with external data – logistics, supplies, sales, customer behavior, etc. Machine Learning algorithms take into consideration a substantial number of factors, starting from weather forecasts and finishing with local political conflicts, which is a mission impossible for a human analyst.
Conclusion
The introduction of complex software systems and technologies to automate a factory and make it “smart” is often a huge challenge for an enterprise and may lead to budget overruns. However, a thougtful approach to enterprise software development makes this process a real game-changer for business. Manufactures all over the world are under huge pressure to make cheaper, better products – faster than competitors – and stay profitable. Investing in the right technology and choosing a reliable software development partner is the key to success.