3D Simulation Software
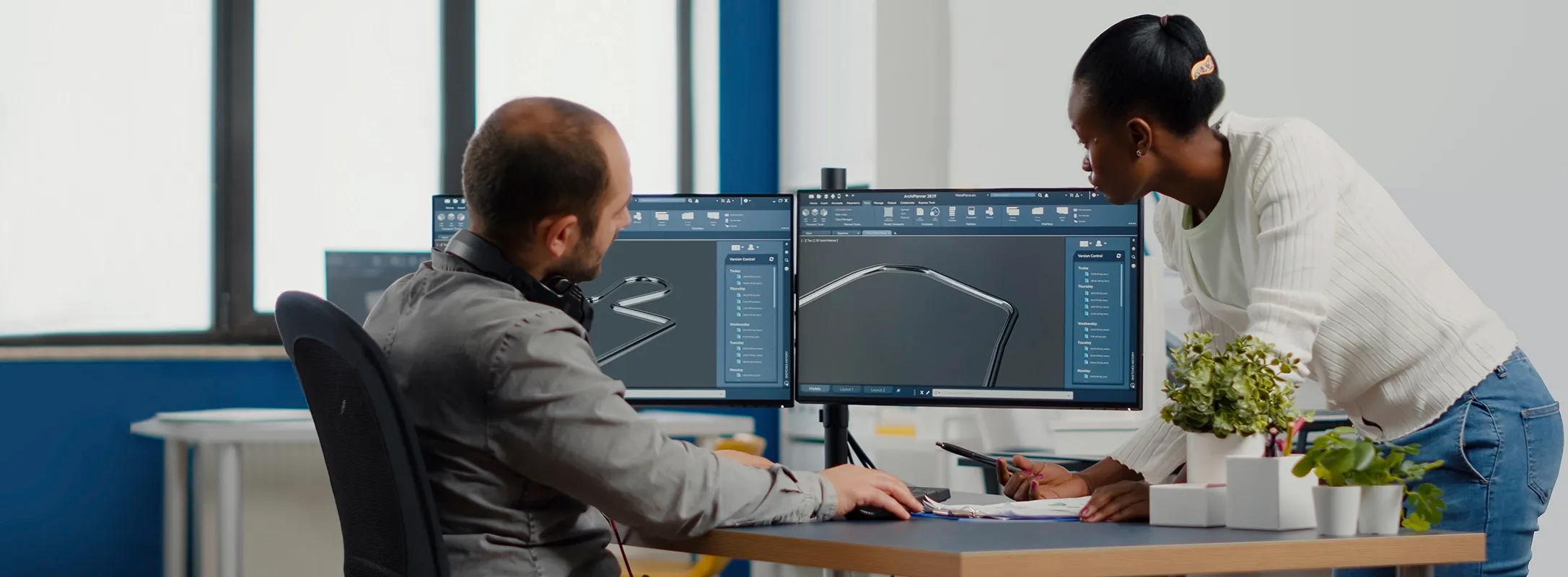
Industry
Industrial automation
Location
USA
Platform
Web
Cooperation
6+ years
About the project
The Client has been producing mechanical, electrical and software engineering solutions in the wire forming and automation industry for half a century. Our project focused on developing software for dedicated high-volume production machines for wire forms and sheet metal stampings. It allows the user to control the machines – track their state in real-time, change the machines’ motor position, create an execution program from scratch, modify the existing one, and then run it on the machine.
Challenge
The complexity of the project was about making the software to properly react to Wire Bending Machine’s (WBM) events: program execution has started / reached instruction number N / paused / ended. There had to be a possibility to perform the simulation without starting a WBM, i.e., execution operations of a WBM should be simulated by the system. Therefore, we used Event-driven Architecture.
Wire bending calculations were among the most difficult tasks. To generate the 3D geometry of a wire, we dealt with reverse engineering of a .PRG file and applied math to values we extracted from it. The goal was to find a 3D path of bent wire considering numerous parameters – wire diameter, tools actual position against cluster’s center point, the rotation angle of wire, bending angle, wire offset. Although all these parameters defined wire bend at the execution step, they also effected previously calculated path’s segments.
Another challenge was adding Open Cascade Technology (OCCT) to the Visual Studio Solution and configuring a build.
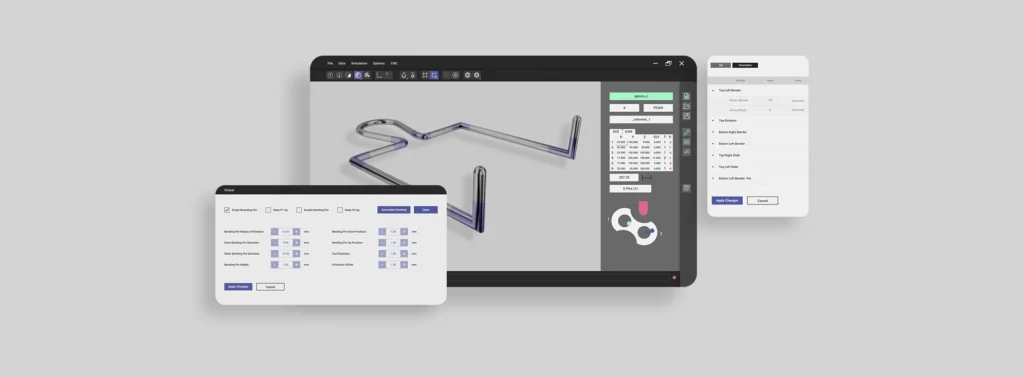
Solution
The application checks feasibility using the simulation of the machine, its separate parts, and tools. The program optimization is done on the screen but not via costly trial and error.
Features
- Virtual 3D motion and simulation of the machine running and production line operations. The software includes a library of ready components that allow running a series of simulations quickly. The user can validate modifications – evaluate how they affect production and see opportunities for improvement.
- Possibility to calculate the manufacturing productivity at the design stage.
- Automatic interference/collision detection – avoiding costly downtime by avoiding collisions.
- Self-correction for interference-free machining: it is necessary to read the tool geometry file
- Easy handling of the data to/from the machine HMI
- Simulation of machining cycle time: the speed is defined by the user
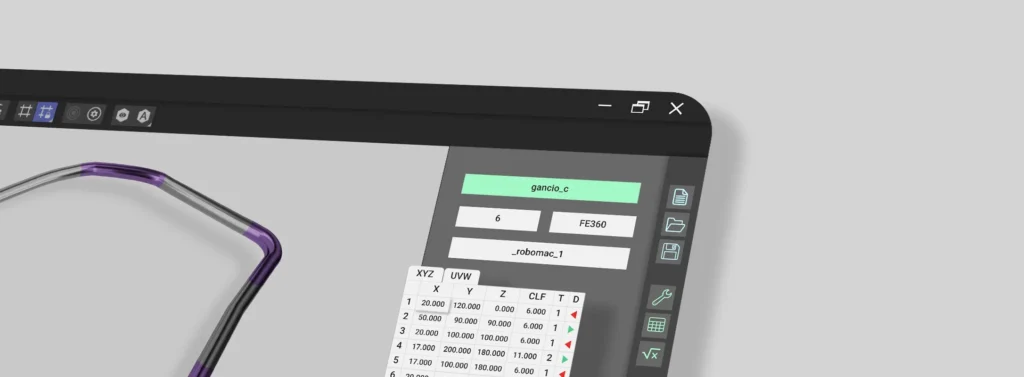
User Interface
- Intuitive navigation
- Convenient keyboard
- Flexible controls
- Undo/redo functionality of the main grid
- Copy/paste functionality of the main grid
- Generation of G-code from temporary grids
- Hidden/shown columns depending on the user’s configuration
Technologies
.NET Core
C#
WPF
Telerik
Business value
The application creates 3D simulations of the production machine performance and manufacturing line operations. It allows the user to avoid errors, which prevents damage and losses, and accurately estimate machine productivity.
All the controls that users need to draw a new part are at fingertips: they just need to enter the wire’s geometric data and let the machine automatically create the program. The manufacturing can be started without any nasty surprises. It also greatly simplifies the operators work. When interference is found in the process, this software executes automatic diagnostic and also provides a solution. The operator can simply follow the selective guidance on the screen to renew the interference-free program, which minimizes human error.
Contact us
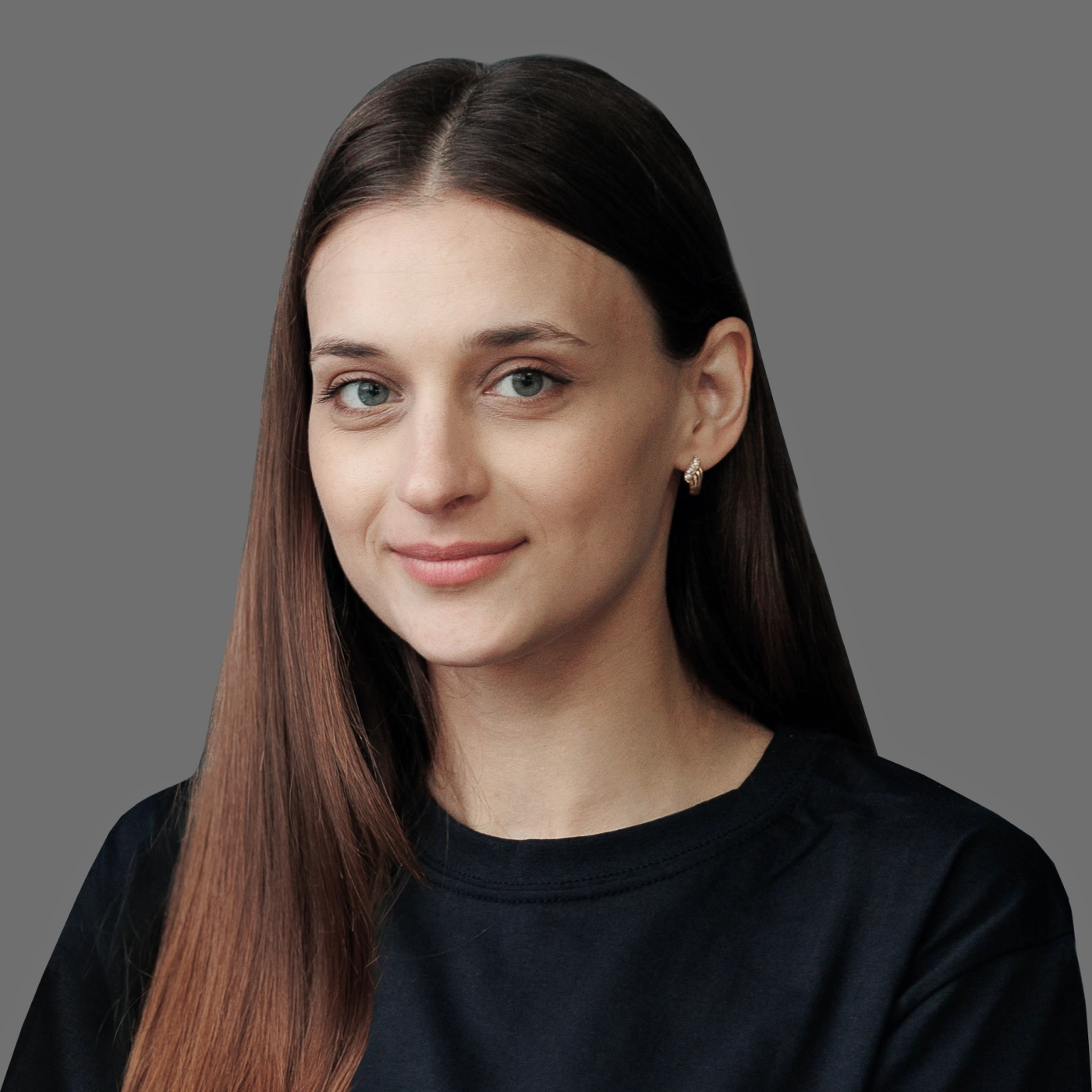
Daryna Chorna
Customer success manager